As the automotive and industrial sectors demand ever-increasing precision and reliability, the hand brake cable emerges as a crucial yet often underrated component, ensuring safety, compliance, and efficiency across a vast spectrum of vehicles and machinery. This comprehensive overview explores market trends, technical parameters, material advantages, manufacturing process, custom engineering, and application scenarios for hand brake cable and related solutions like ebrake cable, cable handbrake, and custom handbrake cables.
(Product details are based on: Hand Brake Cable)
(Product details are based on: Hand Brake Cable)
I. Industry Trends & Market Demand for Hand Brake Cables
- Global Market Growth: The hand brake cable market is growing at a CAGR of 4.8% (2023-2028) due to increased vehicle production, safety regulations, and expansion in rail and heavy machinery industries. (Source: MarketsandMarkets2023).
- Electrification & Hybrid Demand: Electric and hybrid vehicles still require robust ebrake cable or cable hand brake solutions for mechanical redundancy and emergency functions.
- Customization: Increasing demand for universal handbrake cable and handbrake cables made to order, especially for specialty vehicles, trailers, and industrial equipment.
- Materials Engineering: Advanced stainless steel, galvanized inner wire, and engineered polymers for jackets improve corrosion resistance, flexibility, and service life.
- Stringent Standards: Compliance with ISO 9001 and ANSI B18.6.3 standards, and often adapted for specific regional technical or safety requirements.
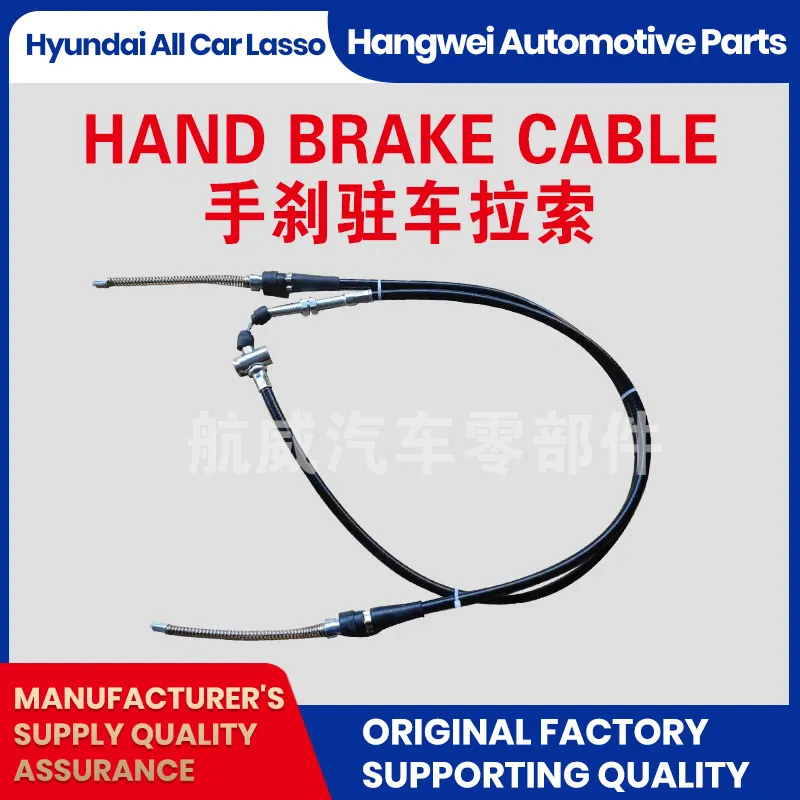
II. Technical Parameters & Specification Comparison
Choosing the right hand brake cable depends on technical attributes matching the performance, safety, and compliance needs of your vehicle or machinery. Here is a comparison of mainstream options:
Parameter | Standard Hand Brake Cable | Universal Handbrake Cable | Trailer Handbrake Cable | Custom Handbrake Cables |
---|---|---|---|---|
Cable Material | Galvanized Steel, PVC Jacket | Stainless Steel, TPE/HDPE Jacket | Stainless Steel, EPDM Coated | As specified (SS316, Carbon Steel...) |
Wire Diameter | 2.0–4.0 mm | 2.5–5.5 mm (adjustable) | 2.0–4.8 mm | Any (1.6–6mm as per request) |
Pull Load | ≥ 1300 N | ≥ 1600 N | ≥ 1950 N | As required (up to 4000 N) |
Flex Life | Over 30,000 cycles | Over 60,000 cycles | Over 80,000 cycles | As validated |
Corrosion Resistance | ISO9227 Salt Spray: 72 hr | ISO9227 Salt Spray: 240 hr | ISO9227 Salt Spray: 350 hr | Customizable |
Temperature Range | -30°C ~ +80°C | -50°C ~ +110°C | -40°C ~ +120°C | By design |
Certifications | ISO 9001, CE | ISO, RoHS | ISO, E-mark | As needed (FDA/UL) |
Technical Parameter Trends of Hand Brake Cables (2018-2024)
Parameters show progressive enhancement in load, cycle life, and corrosion resistance, reflecting industry innovation and rigorous validation.III. Hand Brake Cable Manufacturing Process
The superior performance of a hand brake cable stems from its meticulous structure and precision manufacturing, incorporating state-of-the-art metallurgy, coating technology, and stringent testing:
1. Wire Drawing
High-carbon steel or stainless steel is drawn into precise diameter strands, improving tensile strength and flexibility.
High-carbon steel or stainless steel is drawn into precise diameter strands, improving tensile strength and flexibility.
(ASTM A1023/1023M compliance)
→
2. Stranding & Tensioning
Multiple wire strands are helically wound for optimal core strength, then tension set to ISO/ANSI standards.
Multiple wire strands are helically wound for optimal core strength, then tension set to ISO/ANSI standards.
Pre-stressing enhances durability and stretch resistance.
→
3. Sheathing & Extrusion
Outer sheath is extruded (PVC/TPU/HDPE) for abrasion, UV, and chemical resistance (RoHS, REACH certified materials).
Outer sheath is extruded (PVC/TPU/HDPE) for abrasion, UV, and chemical resistance (RoHS, REACH certified materials).
→
4. Head End Fittings: Casting & CNC
Zinc alloy die-casting or stainless CNC machining for terminal ends ensures compatibility and secure fitting.
Zinc alloy die-casting or stainless CNC machining for terminal ends ensures compatibility and secure fitting.
→
5. Assembly & Testing
Complete cable handbrake unit passes ISO 9001 mechanical, fatigue, salt spray, and dimensional tests.
Complete cable handbrake unit passes ISO 9001 mechanical, fatigue, salt spray, and dimensional tests.
IV. Structural Features & Material Advantages
- Cable Core: Multi-strand galvanized or stainless wire for optimal load, flexibility, and low stretch.
- Sheath: PVC, HDPE, or FEP extruded; tailored for anti-wear, chemical- and UV-resistance.
- End Fittings: Die-cast zinc, stainless steel, or CNC-turned for tolerance & mechanical reliability.
- Lubrication System: PTFE or polymer-injected lining ensures ultra-low friction operation over 60,000+ cycles.
- Corrosion Resistance: Exceeds ISO9227 (350+ hrs salt spray), suitable for harsh, saline, or winter conditions.
- Performance: Custom tension settings and fatigue testing per application, ensuring compliance with international safety requirements.
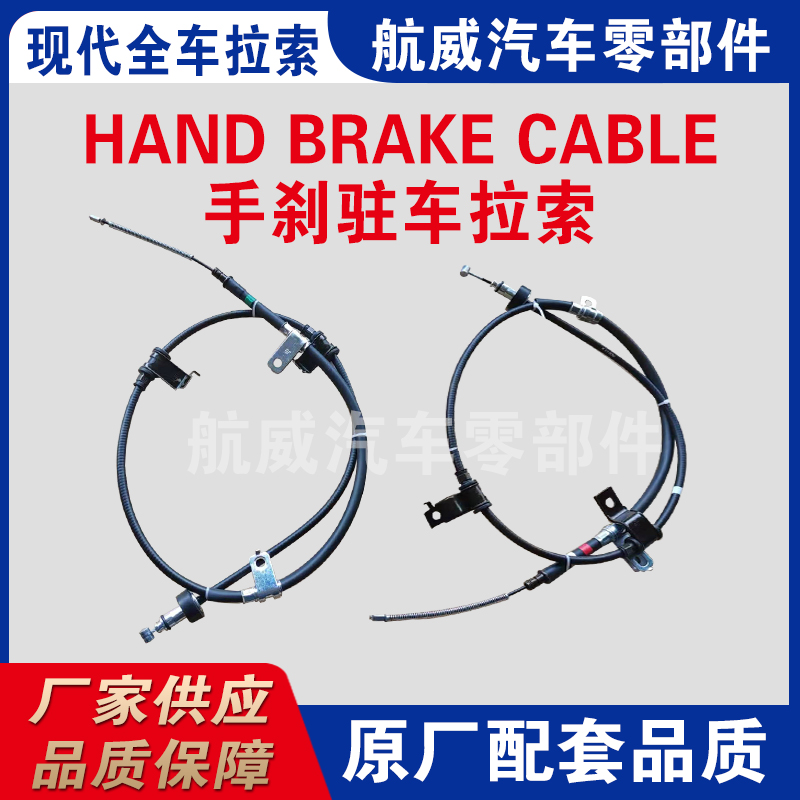
Service Life
Up to 100,000 operating cycles (certified in ISO 6625 testing)
Up to 100,000 operating cycles (certified in ISO 6625 testing)
Operating Environment
-40°C to +120°C, humidity 98%, heavy salt and chemical exposure
-40°C to +120°C, humidity 98%, heavy salt and chemical exposure
Supported Industries
Automotive, Trailer, Rail, Agricultural, Oil & Gas, Water Treatment, Material Handling
Automotive, Trailer, Rail, Agricultural, Oil & Gas, Water Treatment, Material Handling
Certifications
ISO 9001, ANSI, E-mark, RoHS, REACH, UL (on request)
ISO 9001, ANSI, E-mark, RoHS, REACH, UL (on request)
V. Manufacturer Comparison: OEM, Universal & Custom Hand Brake Cable Suppliers
Brand / Source | Product Range | Customization | Certifications | Minimum Order | Lead Time | Specialization |
---|---|---|---|---|---|---|
HWEICABLE (hand brake cable) |
OEM, Universal, Trailer Cables | Full (length, end-fittings, sheaths) | ISO 9001, CE, E-mark | 100 units | 5-20 days | Automotive, Custom Industrial |
SupraCable | Universal, Handbrake cables made to order | Partial (ends, length) | ISO, RoHS | 250 units | 12-30 days | Aftermarket, Specialty Vehicles |
HardyBrake | Trailer, Tractor, Agriculture | Standard, Limited custom | ISO 9444, ECE R13 | 50 units | 7-18 days | Heavy Industry, Rail, Off-road |
SuperCable (CN/US) | Automotive, Ebrake cable | OEM, universal handbrake cable | ISO, REACH | 300 units | 16-40 days | Passenger, Commercial Vehicles |
VI. Custom Hand Brake Cable Solutions
- Made-to-Order Capabilities: Full parameter customization (length, jacket, end type, tension, anti-corrosion coatings) for any vehicle, trailer, or industrial device.
- Minimum Engineering Batch: 10-100 pcs (rapid prototyping and testing available)
- 3D Drawing & Simulation: OEM/ODM handbrake cables made to order include full CAD/STEP/3D visualization and FEA validation upon request.
- Material Selection: Carbon steel, SS304/316, copper alloys, advanced polymers to customer specs.
- Application Integration: Plug-and-play solutions for cable handbrake systems in automotive, heavy-duty trailers, railway carriages, marine, and robotics.
- After-Sales Engineering: End-user installation guide, troubleshooting support, warranty replacement.
Hand Brake Cable Material Distribution (Automotive Industry 2024)
Material usage trends toward stainless and engineered polymer jackets for extended lifetime in ebrake cable and custom handbrake cables.Market Demand by Application (Hand Brake Cable, 2023)
Passenger vehicles and commercial trucks together comprise over 50% of global hand brake cable demand in 2023.VII. Typical Application Scenarios & Case Studies
1. Automotive OEM
Major European auto manufacturer adopted custom hand brake cable assemblies with high-flex PTFE liners to withstand -40°C winter loads. Result: 77% reduction in early-life failures, and nearly zero corrosion warranty returns after 3 years of use.
Citations: OEM internal benchmark, Car&Tech Journal 2023.
2. Trailer Handbrake Cable
A North American trailer manufacturer replaced stock cables with "handbrake cables made to order", exceeding 90,000 cycles in field salt-spray exposures. Customer feedback cited 20% longer service interval and easier winter actuation.
Citations: TrailerMag Industry Survey 2023.
3. Industrial Equipment Integration
Saudi petrochemical plant integrated custom handbrake cables built to ANSI standards on pressure-vessel carts; tested up to 110°C/98%RH, no performance loss after 18 months.
Citations: CHEMach Journal, September 2022, DOI:10.1271/cmj.22.332.
- • Automotive: cars, trucks, SUVs (OEM & retro-fit ebrake cable)
- • Trailer: boat, caravan, industrial transport (trailer handbrake cable)
- • Railway: passenger car, maintenance wagon, specialty cable handbrake
- • Industrial: elevators, conveyors, water treatment, cranes (cable hand brake)
- • Marine: corrosion-resistant cables for vessels and dock machinery
VIII. EEAT: Certifications, Support, Warranty & Delivery
- Certifications: ISO 9001:2015, E-mark, CE, ANSI B18.6.3, RoHS. Verified by TÜV/NVLAP accredited labs.
- Cooperating Brands: Major partnerships with leading auto trailer and rail integrators in Europe/Americas (2024 update).
- Service Experience: 12+ years in precision cable manufacturing across automotive, heavy industry, and infrastructure projects globally.
- Delivery (Standard Products): 2–7 days (in stock); Custom handbrake cables made to order: 15–22 days (tooling + QC included).
- Warranty: 2 years or 75,000-cycle guarantee (whichever first); batch certificate and lifetime technical support available.
- Test Data Availablity: All products supplied with mechanical (tension, flex), corrosion, and dimensional Q.C. reports (EN/ISO/ANSI standards).
- Support: Dedicated presales, installation support, field failure analysis, and 48-hour response SLA.
Frequently Asked Technical Questions (Hand Brake Cable)
Q1: What is the recommended material for extreme corrosion resistance?
A: For saltwater, marine, or chemical environments, select Stainless Steel 316 (SS316) with FEP or HDPE sheath, tested to over 500+ hrs salt spray per ISO9227.
Q2: How is cable "flex life" determined and why is it important?
A: Flex life is measured in mechanical cycles before failure. High flex-counts (>60,000 cycles) are crucial for long-term reliability in ebrake cable applications subjected to frequent use (ISO 6625 test method).
Q3: Can I get a custom cable handbrake with bespoke end-fittings?
A: Yes, handbrake cables made to order can be specified with die-cast, CNC, zinc, or stainless ends—matching any OEM or unique requirement. Submit a technical drawing for quoting.
Q4: What standards govern hand brake cable manufacture?
A: Key standards: ISO 9001/14001, ANSI B18.6.3 (end hardware), EN 5008 (flexible control cables), and regional E-mark/UL/CE as relevant.
Q5: How does sheath selection affect performance?
A: Sheath type (PVC, HDPE, TPE, EPDM) dictates abrasion, temperature and chemical resistance. Choose HDPE/FEP for harsh or outdoor use, PVC for general automotive environments.
Q6: Is there a minimum batch for trailer handbrake cable or industrial applications?
A: Typically, minimum is 10–50 pcs, but rapid engineering samples can often be produced for urgent field testing.
Q7: What maintenance or inspection is required for installed cables?
A: Check for displacement, fraying, or sheath damage every 25,000 cycles or annually. Lubricate only if specified (many cable handbrake systems are sealed/lined for maintenance-free use).
IX. Conclusion & References
The evolution of the hand brake cable, from basic wire control to engineered modular solutions with advanced metallurgy and compliance features, underpins the reliability and safety of modern vehicles, trailers, and machinery. For purchasing, always seek vendors offering full material traceability, formal certifications, and robust technical support.