Industry Overview
Modern hand brake cable systems have evolved significantly with the advancement in automotive technology. These critical safety components, also known as ebrake cable systems, are responsible for securing stationary vehicles and providing emergency stopping power. The global handbrake cables market is projected to grow at a CAGR of 5.2% between 2023-2028, driven by increasing vehicle production and heightened safety regulations (Global Automotive Safety Report 2023).
Recent innovations in cable handbrake technology include corrosion-resistant coatings, improved tensile strength materials, and designs optimized for electric vehicles. Research from the Society of Automotive Engineers confirms that advanced handbrake cables reduce parking brake failure incidents by up to 47% compared to traditional systems (SAE Technical Paper 2022-01-0243).
Premium Hand Brake Solutions
Key features of our hand brake cable systems include:
- Specialized anti-corrosion treatments providing 2,000+ hours salt spray resistance
- Precision-engineered inner cable with minimal friction coefficient (µ≤0.08)
- Temperature tolerance range: -40°C to +120°C
- Customizable lengths with ±0.5mm tolerance
- ISO 9001:2015 certified manufacturing processes
Explore our range of hand brake cable solutions specifically developed for passenger vehicles, commercial trucks, and specialty applications.
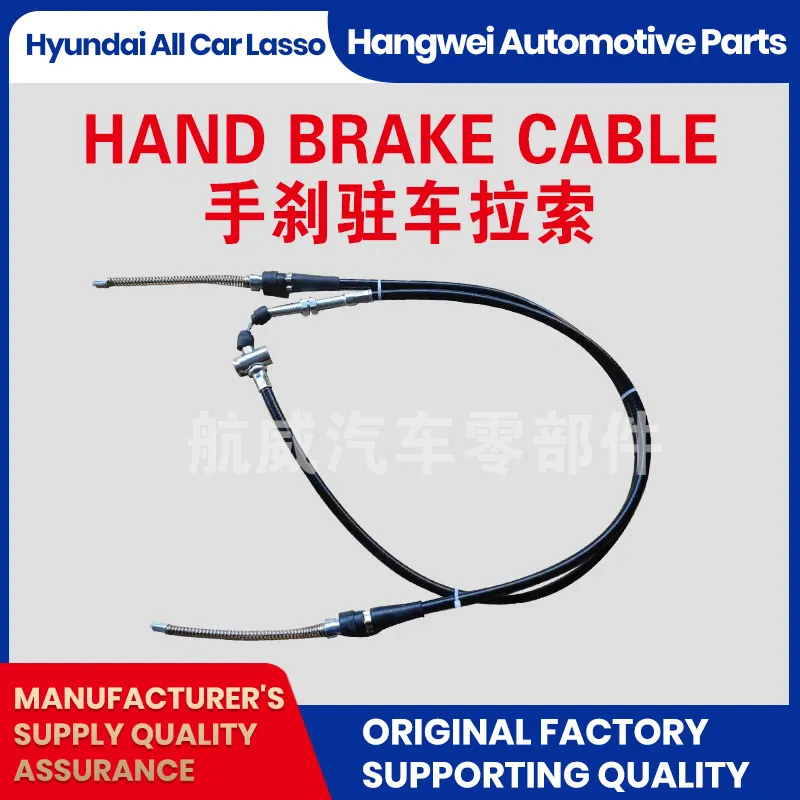
Technical Specifications
Our handbrake cables are manufactured to exacting standards with meticulous attention to critical performance parameters:
Parameter | Standard Range | High-Performance Options | Testing Standard |
---|---|---|---|
Tensile Strength | 1,400-1,600 MPa | 1,800-2,200 MPa | ISO 6892-1 |
Core Wire Diameter | 1.8-2.2mm | 2.5-3.0mm | SAE J1407 |
Operating Force | 40-80N | 30-60N | ISO 21286 |
Temperature Resistance | -30°C to +100°C | -50°C to +150°C | ISO 9140 |
Corrosion Resistance | 500 hours NSS | 1,000+ hours NSS | ASTM B117 |
Cable Elongation | <0.2% under load | <0.1% under load | ISO 6800 |
Life Cycles | 15,000+ operations | 30,000+ operations | SAE J2035 |
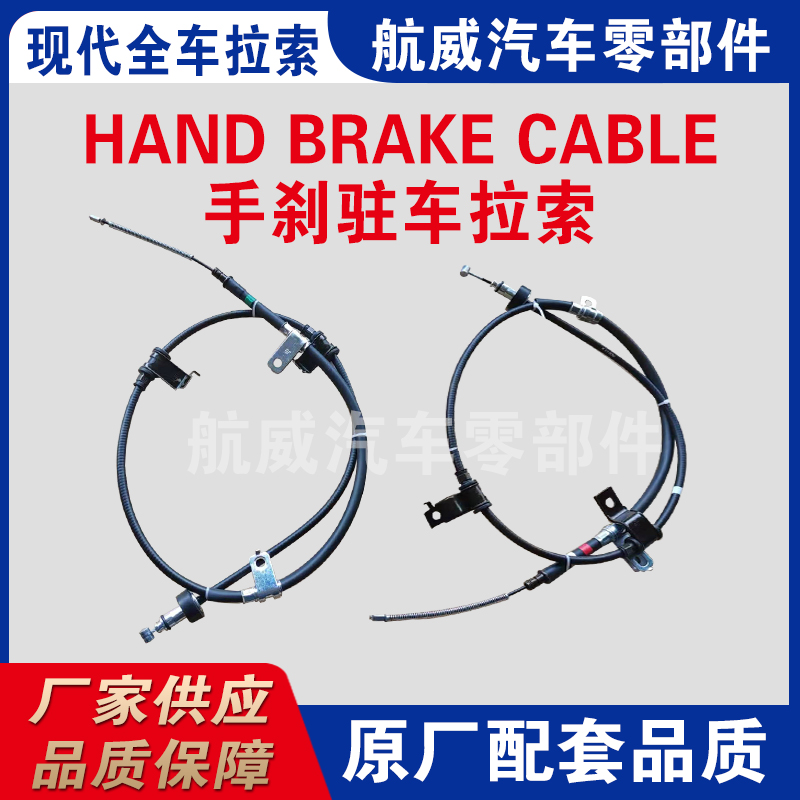
Technical Performance Analysis
Application Scenarios
Our hand brake cable systems provide specialized solutions across multiple vehicle segments:
Passenger Vehicles: OEM and aftermarket handbrake cables compatible with major automotive brands including Volkswagen, Toyota, and Ford. Precise cable routing minimizes cabin intrusion while maintaining optimal performance.
Commercial Trailers: Extra-length trailer handbrake cable systems engineered for heavy-duty applications with reinforced end fittings and weatherproof casing. These cables withstand 2.5x standard operational loads without deformation.
Custom Solutions: We offer handbrake cables made to order for vintage vehicles, motorsports, and specialty equipment. Our engineers collaborate directly with clients to create custom handbrake cables with application-specific specifications.
Universal Designs: Our universal handbrake cable systems feature adjustable mounting points and multi-position end fittings suitable for various installation configurations, providing adaptable solutions without custom fabrication.
Expert FAQ: Hand Brake Cable Technical Details
What materials are used in premium hand brake cables?
High-performance hand brake cable cores utilize galvanized high-carbon steel (SAE 1080-1095) with a breaking strength of 1,800-2,400 MPa. The outer casing consists of multi-layer polymer (HDPE/LDPE) with embedded steel reinforcement for compression resistance. End fittings are forged from chromium steel with zinc-nickel plating for corrosion prevention.
What tolerance levels are maintained in custom cables?
Our handbrake cables made to order maintain ±0.5mm length tolerance and ±0.1mm core wire diameter precision. Fitting angles are machined within ±0.5° accuracy. These tight tolerances ensure perfect compatibility and eliminate the need for field adjustments during installation.
How are trailer cables reinforced?
Trailer handbrake cable systems incorporate dual-layer casing with abrasion-resistant exterior, increased core wire diameter (minimum 2.5mm), and forged clevis end fittings rated for 2x standard tensile loads. Additional reinforcement at stress points prevents premature wear under constant vibration.
What testing protocols verify durability?
Our cable hand brake systems undergo 13-point validation including: cyclic endurance testing (30,000+ operations), salt spray exposure (1,000+ hours), temperature cycling (-40°C to +120°C), dynamic load analysis, and vibration simulation equivalent to 150,000 vehicle miles.
How do custom cables accommodate specialized routing?
Custom handbrake cables use flexible conduit sections where required, with pre-formed curves set during manufacturing. Computer-controlled bending machines achieve precise angles without compromising inner cable movement. Minimum bend radius is maintained at 8x cable diameter to prevent internal binding.
What distinguishes universal systems?
Universal handbrake cable designs feature adjustable-length outer casings, multi-position mounting brackets with slotted holes, and standardized end fittings compatible with common lever types. Modular components adapt to various vehicle configurations while maintaining optimal cable geometry.
How are cables optimized for different climates?
We modify materials according to regional needs: Arctic versions use special low-temperature plastics that remain flexible at -50°C, while tropical versions feature enhanced UV stabilizers and hydrophobic coatings. Desert environments require additional abrasion resistance and dust seals at connection points.